Short Courses
Reconciliation - Getting it Right the First Time
Level: Intermediate
Facilitators: Clementine Clark, Danny Tolmer, Snowden Optiro
FULL DAY – Saturday, October 19th, 08:30 to 16:30
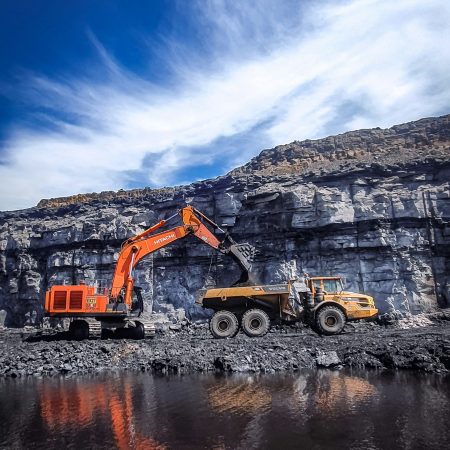
In this 1-day course we cover all aspects of the reconciliation process, including the key data which needs to be collected, the importance of unbiased measurement of volumes, tonnages and grades (among other metrics). We will show how to map out the production data flow and discuss the important measures of performance. Attendees will work on real-life reconciliation information and examine the potential sources of error. Scrutiny of the processing side of the reconciliation information provides another perspective, and a discussion of best practice highlights how efficient and useful a well-specified system can be.
Course Outline:
- Overview of the reconciliation cycle; why are we doing it anyway? The stakeholders’ expectations and whether we can meet them.
- Sources of measurement and sources of error for open pit and underground mines; reducing error and automating the measurement.
- What are the key metrics for reconciliation? Do we provide too much useless information?
- Working with and analyzing real-world production data.
- What happens at the plant? How does this influence what happens at the mine?
- Mapping out production data flows, designing and simplifying reconciliation systems.
- Best practice in reconciliation; how to get there and the alternatives.
During the course you will:
- Discuss the fundamentals of reconciliation – what are we trying to achieve and what do the various stakeholders want?
- Derive some of the key metrics from real production data sets and discuss their usefulness.
- Appreciate how to present information simply and how to make the most of graphics.
- Understand the key sources of error in the reconciliation cycle and how to reduce/eliminate.
- Learn how to map, streamline and improve production flow systems.
- Appreciate best practice in reconciliation systems and how to achieve it.
Short Course Objectives:
Key topics covered, to achieve best practice, are: Overview of the reconciliation cycle; why are we doing it anyway? The stakeholders’ expectations and whether we can meet them. Sources of measurement and sources of error for open pit and underground mines; reducing error and automating the measurement. What are the key metrics for reconciliation? Do we provide too much useless information? Working with and analyzing real-world production data. What happens at the plant? How does this influence what happens at the mine? Mapping out production data flows, designing and simplifying reconciliation systems. Best practice in reconciliation; how to get there and the alternatives.
Target Audience:
These are the stakeholders who are responsible and interested in good reconciliation systems: The company CEO/MD (responsible to board and shareholders) – Overall responsibility The company CFO (responsible to CEO and board) – Financial/commercial responsibility The company COO (responsible to CEO) – Operational responsibility – all mines and plants (and smelters) The operation’s General Manager (responsible to COO) – Responsibility at the operational level (mine/plant) The Marketing Team (responsible to the MD or COO) – Responsibility for products to clients The Mining Manager (responsible to General Manager) – Mine production responsibility The Mill Manager/Superintendent (responsible to General Manager) – Responsibility for recovery and the quality of the product(s) The Senior Mine Planning Engineer (responsible to the Mining Manager or the General Manager) – Responsible for long-term to short-term predictions The Geology Superintendent/Geology Manager (responsible to General Manager) – Responsible for the grade control or resource models The Senior Mine Geologist (responsible to the Chief Geologist or to the Mining Manager) – Generally does the mine reconciliation.
About the Instructors:
Clementine Clark (primary presenter) – BSc(Geo), Citation Programme in Applied Geostatistics. Associate Principal Consultant – Vancouver – Snowden Optiro
Clementine is a skilled Resource Geologist proficient in data analysis, geological modeling, and resource estimation. She specializes in various software tools such as Supervisor, Datamine, and Leapfrog for comprehensive analysis and modeling. With experience spanning across Africa and the Americas, Clementine is recognized as a Competent Person in Platinum Group Element (PGE) and related deposits. Key Specializations: Resource estimation using techniques like Inverse Distance, Ordinary Kriging, MIK, and Conditional Simulation. Projects encompass geological modeling, Mineral Resource estimation, QAQC training, and technical audits. Expertise extends to copper-cobalt, gold, and polymetallic skarn deposits, as well as chrome, manganese phosphates, and vanadium. Notable Contributions: Leading professional development courses at Snowden Optiro. Delivering comprehensive exploration plans, project valuations, and reconciliation reviews. Clementine’s Work Portfolio: PGE, Base Metal, and Silver projects across diverse geographies. Significant contributions to exploration plans, project valuations, and technical audits.
Danny Tolmer (co-presenter) P.Eng., BASc. Regional Manager – North America – Snowden Optiro
Danny has more than 20 years of mine operational and consulting experience specializing in both open pit and underground mine optimization. He has experience in project economic evaluation, open pit drill and blast, short- and long-term mine planning, design, and site supervision. He has specialist skills in project management and has completed all levels of project studies from conceptual to feasibility. His consulting assignments have included numerous technical studies, audits, M&A due diligence, and mine operational assistance. He has completed numerous studies comparing conventional truck and shovel with various material handling technologies. His commodity experience includes coal, copper, diamonds, gold, silver, nickel, lead, zinc, uranium, limestone, rare earth, and specialty industrial aggregates such as fracsand. Danny is a professional mining engineer currently registered with EGBC, APEGA, APEY, NAPEG, and PEO. Danny is a Qualified Person for open pit mining for NI43-101 and SK1300 Technical Reporting, covering most commodities including: Diamonds, Coal met/thermal, Gold, Copper, Nickle, Uranium, Lithium, Graphite, and Industrial Minerals – Limestone, Phosphate, Potash, Silica, Quartzite, and Frac sand.